Preventing Weld Undercut: Proven Approaches Every Welder Need To Know
Wiki Article
Grasping the Art of Welding: Just How to Prevent Undercut Welding Issues for Flawless Manufacture Results
By comprehending the root triggers of undercut welding and executing efficient methods to prevent it, welders can raise their craft to brand-new levels of quality. In the quest of flawless construction outcomes, understanding the art of welding to avoid undercut concerns is not simply a skill however a requirement for those aiming for perfection in their job.Understanding Undercut Welding
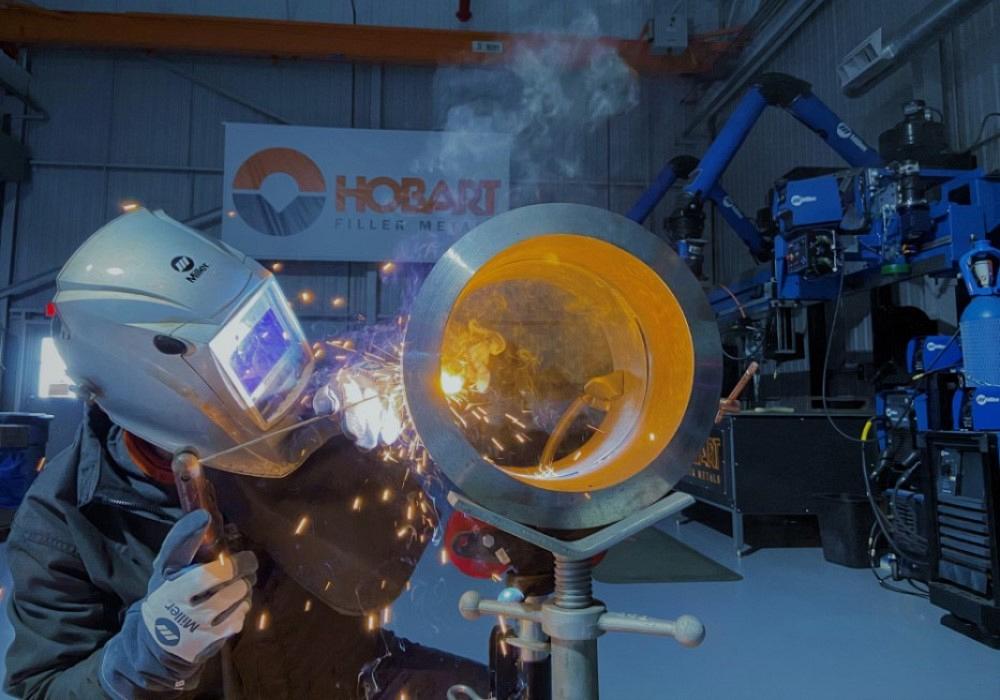
To avoid undercut welding, welders ought to guarantee correct welding criteria, such as changing the present, voltage, travel rate, and keeping the right electrode angle. By comprehending the causes of undercut welding and applying precautionary measures, welders can accomplish premium, structurally audio welds.
Reasons of Undercut in Welding
Understanding the factors that add to undercut in welding is vital for welders to produce high-grade, structurally sound welds. When the weld metal does not properly load the groove formed in between the base steel and the formerly transferred weld steel, undercutting occurs. A number of variables can bring about damage in welding. One usual reason is too much warmth input. Welding at high temperature levels for prolonged durations can result in the base steel thawing even more than wanted, leading to undercut. Poor welding incorrect or present welding speed can likewise add to damage. Inadequate current may not give enough warm to thaw the base and filler metals sufficiently, while extreme rate can prevent proper fusion, creating undercut. Furthermore, incorrect electrode angles or wrong lantern adjustment methods can develop locations of reduced weld metal deposition, promoting undercut. Recognizing these reasons and carrying out appropriate welding techniques can aid stop undercutting problems, ensuring durable and solid welds.Strategies to Stop Undercutting

To mitigate the threat of undercutting in welding, welders can utilize calculated welding methods targeted at boosting the high quality and honesty of the weld joints. One reliable technique is to readjust the welding specifications, such as voltage, existing, and travel speed, to guarantee appropriate warmth input and deposition. Keeping an appropriate electrode angle and ensuring constant travel rate can likewise aid stop undercut. In addition, using the appropriate welding technique for the details joint configuration, such as weave or stringer grains, can add to decreasing undercutting. Preventing weld undercut.
Employing back-step welding techniques and managing the weld grain account can likewise aid disperse warmth uniformly and reduce the risk of undercut. Regular assessment of the weld joint throughout and after welding, as well as implementing quality assurance procedures, can aid in spotting and resolving damaging problems promptly.
Relevance of Proper Welding Parameters
Selecting and preserving appropriate welding criteria is necessary for achieving successful welds with marginal problems. Welding criteria refer to variables such as voltage, existing, travel speed, electrode angle, and securing gas flow price that directly impact the welding process. These specifications need to be thoroughly adjusted based upon the sort of product being welded, its density, and the welding technique utilized.Correct welding specifications make sure Continue the correct amount of heat is put on melt the base steels and filler product consistently. If the specifications are set too expensive, it can cause excessive warmth input, triggering spatter, burn-through, or distortion. On the various other hand, if the parameters are too reduced, incomplete blend, lack of infiltration, or undercutting may take place.
High Quality Guarantee in Welding Procedures
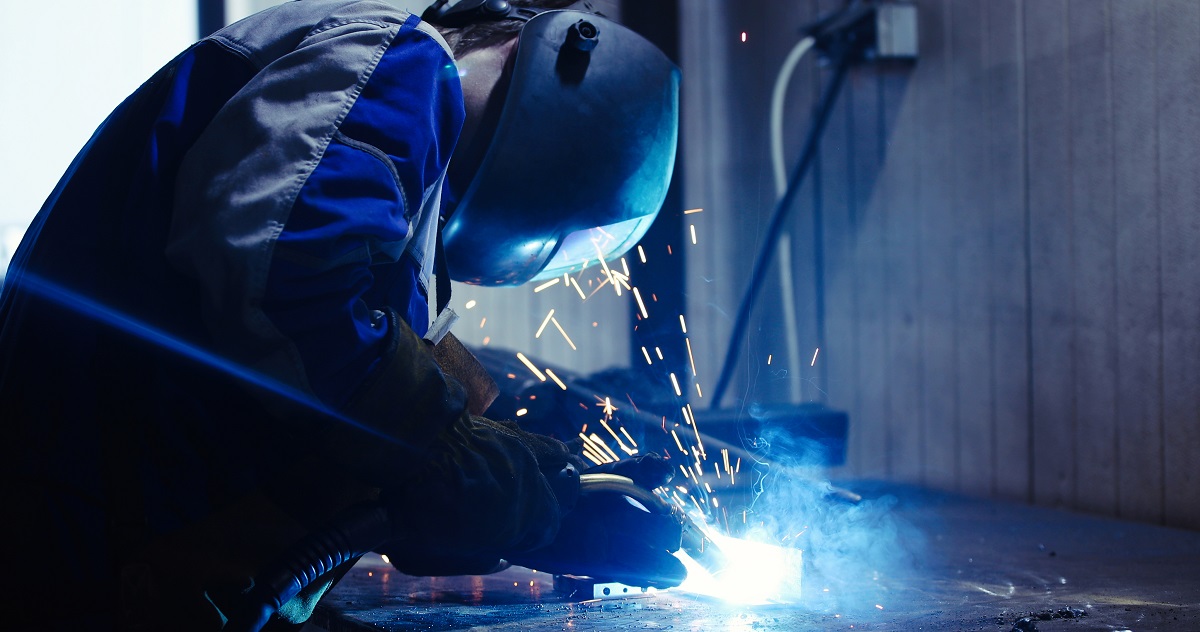
Conclusion
In final thought, understanding the art of welding needs a complete understanding of undercut welding, its causes, and methods to avoid it. By guaranteeing correct welding parameters and carrying out top quality guarantee practices, flawless manufacture outcomes can be achieved. It is vital for welders to constantly strive for excellence in their welding operations to stay clear of undercut find more concerns and create high-quality welds.Undercut welding, a typical issue in welding procedures, occurs when the weld steel doesn't properly fill the groove and leaves a groove or depression along the welded joint.To avoid undercut welding, welders should guarantee appropriate welding specifications, such as changing the current, voltage, traveling rate, and maintaining the correct electrode angle. Insufficient welding inaccurate or existing welding rate can also add to damage.To minimize the risk of undercutting in visit here welding, welders can use tactical welding strategies aimed at boosting the high quality and honesty of the weld joints.In final thought, mastering the art of welding calls for a detailed understanding of undercut welding, its reasons, and strategies to prevent it.
Report this wiki page